Ultrasonic phased arrays is a novel technique for generating, receiving and imaging ultrasound. PAUT use multiple ultrasonic elements and electronic time delays to create beams by constructive and destructive interference. As such, it offer significant technical advantages for weld testing and plant monitoring over conventional ultrasonic as phased array beams can be steered, scanned, swept and focused electronically from a fixed probe position. Beam steering permits the selected beam angles to be optimized ultrasonically by orienting or focusing them perpendicular to the predicted discontinuities. Phased arrays allow real-time control of three important ultrasonic probe parameters: Focal distance & Beam angle: continuously and dynamically adjustable, Focal spot size: dynamical-ly adjustable
Renu’s Advance NDE Services
Paut Inspection
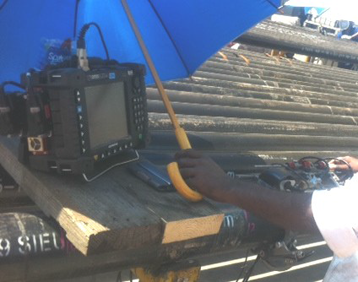
Additional benefits:
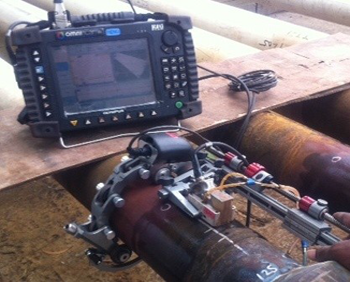
TOFD Inspection
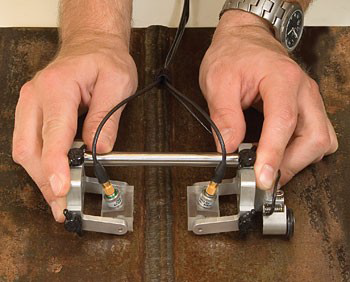
TOFD Utilizes diffracted energy in the detection of flaws; the technique is less reliant on flaw orientation and morphology than standard pulse echo techniques, leading to improved sizing and probability of defect detection (PPOD). Additionally, computerized electronic data capture and storage, in conjunction with scanning manipulators enable rapid scanning speeds to be achieved TOFD has now been accepted as an alternative to Radiography in Pre-Service Inspections with standards such as ASME 2235, and its use in pipe weld and thick walled pressure vessel fabrication is now common place.
TOFD Advantages :
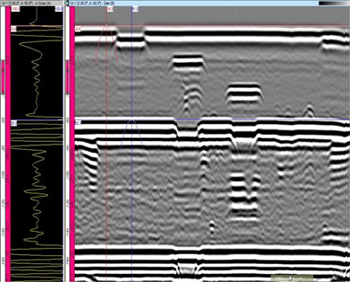
EDDY Current Inspection

In an eddy current testing a circular coil carrying current is placed in proximity to the test specimen .The alternating current in the coil generates changing magnetic field which inter-acts with test specimen and generates eddy current. Variations in the phase and magnitude of these eddy currents and variations in the electrical conductivity or magnetic permeability of the test object, or the presence of any flaws, will cause a change in eddy current and a corre-sponding change in the phase and amplitude of the measured current.
ET Advantages:
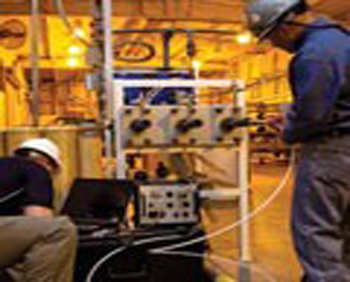
ACFM Inspection
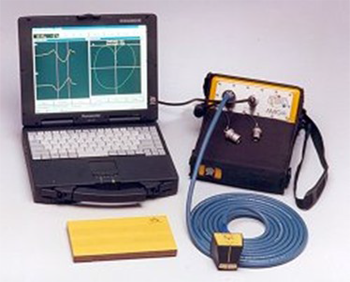
The Alternating Current Field Measurement technique is an electromagnetic technique capable of both detecting and sizing (length and depth) surface breaking cracks in metals. The alternating constant current in a tangential solenoid, remote from the test surface, induces electric currents in the sample surface which are uni-directional and of uniform strength over a localized area under the solenoid.
ACFM Advantages:
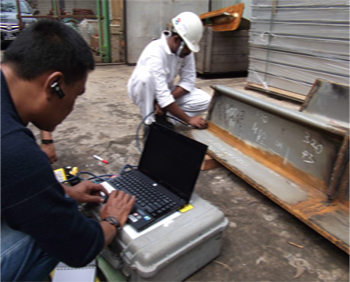
IRIS Inspection
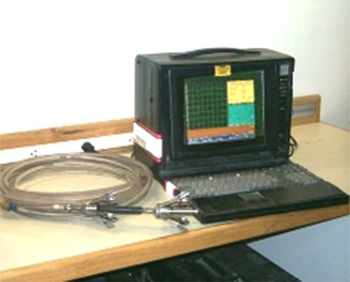
IRIS (Internal Rotary Inspection System) is a measuring system to measure the exact thick-ness of both ferrous and non-ferrous tubes of exchangers, air fins, coolers, boilers and other similar equipment. Most exchangers are sensitive for internal and/or external corrosion.
IRIS Advantages:
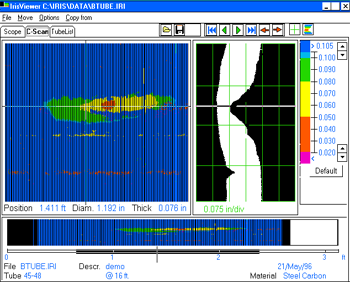
Ultrasonic C-Scan Inspection
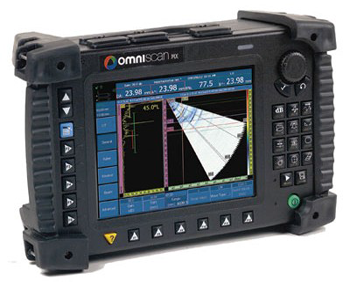
Advance Ultrasonic Corrosion Mapping is a key method in most non-invasive inspection strategies. In order to inspect the range of components e.g. pipes, vessels, tanks etc. Energy Workforce uses multiple types of Ultrasonic Corrosion Mapping which is versatile to pro-vide accurate and reproducible fingerprints of material integrity.
C- Scan Advantages:
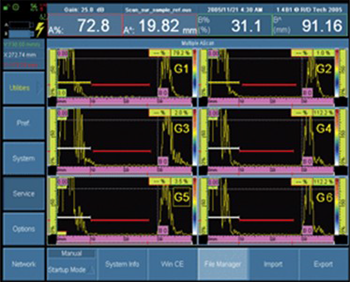
LRUT Inspection
LRUT is used to detect corrosion, erosion in pipe work. An array of transducers is clamped around the pipe and ultrasound is transmitted simultaneously along the pipe in both directions. The return signal is received by the same transducers, and the data are analyzed using the system’s calibrated software.
The technique’s principal advantage is that it provides 100% initial screening cov-erage, and only requires local access to the pipe surface where the transducer array is to be attached. The technique has the ability to inspect inaccessible areas such as clamps and cased or buried pipes. It works without the need to remove insulation or coating.
C- Scan Advantages:
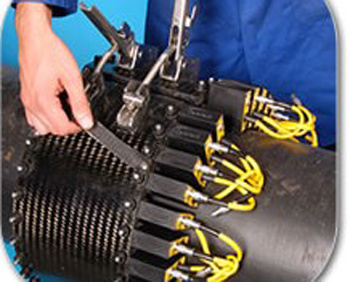